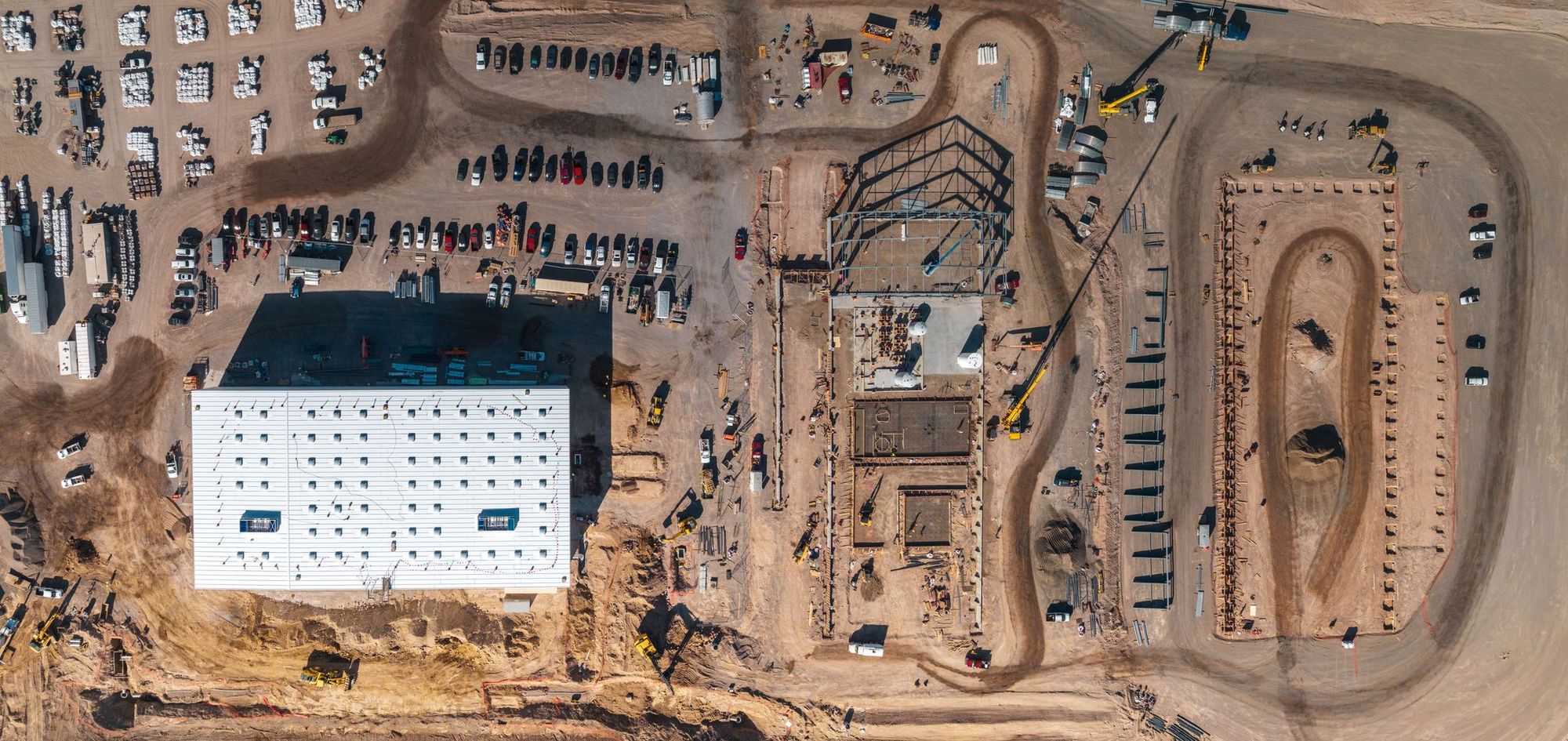
Jan 19, 2022
An update on our anode copper foil product & facility
Read post
Redwood’s mission is to increase sustainable battery materials production and build these materials from an increasing amount of recycled content. The key component in a lithium-ion battery is the cathode active material which is primarily responsible for determining the battery performance, safety, and cost. Redwood’s very high recycled content makes it the most sustainable battery material available on earth. Cathode is the single most expensive and important component in an EV, containing all the lithium, cobalt, and nickel that is critical in a lithium-ion battery.
Cathode materials have a long and complex supply chain that typically involves mining and refining metal feedstocks, manufacturing cathode precursors, and then, final production of cathode active materials. One difficulty in manufacturing cathode active materials is the sensitivity to a precision process and manufacturing conditions. In particular, the manufacturing of cathode precursor and cathode materials are inherently interdependent, with many of the final properties determined during the manufacture of the precursor materials. In a typical process, metal sulfates (nickel, cobalt, manganese and/or aluminum) are used to manufacture precursor materials via co-precipitation. These precursor materials are then combined with lithium salt and calcined to manufacture the final cathode active materials. Key to enabling a circular, domestic supply chain for cathode is the ability to regain original materials performance from recycled feedstock.
The economics are compelling for recycled content; we’re already producing material at a cost competitive with virgin mined metal. Since cathode produced from recycled content is new and growing, the industry must gain confidence in the physiochemical and electrochemical properties of cathode from recycled metals.
The U.S. Department of Energy’s Argonne National Laboratory is a renowned institute of research in science and engineering. The Materials Research Group at Argonne, which specializes in the design, synthesis, and advanced characterization of cathode materials as well the electrochemical testing of full-cell systems, recently completed a collaborative effort to verify the performance of high-nickel cathodes (NMC-811) using cathode precursors from Redwood’s recycling process.
Argonne tested Redwood’s recycled metal-sulfates to validate the performance of the cathode material when put into the production of battery cells.
Various metal-sulfates, synthesized by the Redwood team, were used by the Argonne team to synthesize NMC-811 cathode, via co-precipitation of metal-hydroxides from the precursors, in continuous stirred tank reactors – a method that is reflective of current state-of-the-art industrial production. Standardized electrochemical protocols, developed by research programs within the U.S. Department of Energy's Vehicle Technologies Office, were then used to test the performance of the final NMC-811 electrodes.
Results showed identical cycle-life performance, discharge capacity and Coulombic efficiency between cathode materials made from metal-sulfates from virgin mined metals and those synthesized from recycled materials by Redwood. Furthermore, rate capability and area-specific impedance measurements even showed an advantage when using certain Redwood metal-sulfates.
Argonne concluded “pristine performance can readily be obtained” from Redwood’s recycled metal-sulfates and will have higher capacity and lower direct current internal resistance. We’re grateful to the Argonne team for conducting this collaborative work and we are as excited as ever about a circular, sustainable future.